Furnaces
Use CFD modeling to improve burner design and operation
Process heaters are essential pieces of equipment in the refining and petrochemical industry that are used to heat hydrocarbons to a desired temperature.
Alternatives to ladders and platforms for inspection and maintenance of elevated flare tips
Flare systems are used in refineries and chemical plants as a last line of defense for the plant by burning all unwanted gases and liquid during any upset or emergency condition.
Cost-effective naphtha hydrotreating unit revamp to increase high-octane reformate production
India, which is the third-largest economy in the world, is home to nearly 18% of the world’s population (nearly 1.4 B).
Apply ceramic coatings to extend radiant tube life in process heaters
Process tubes in refining applications are typically steel alloy (ASTM A335 P22, P5 or P9), which contain 2.25%, 5% and 9% Cr, respectively. These grades oxidize at operating temperatures, and scale will grow continuously on the surface, often reaching 2 mm in thickness in higher-temperature/high-heat-flux units. The layers of scale are very insulating and represent a significant barrier to conductive heat transfer to the process.
Case study: Heat exchanger tube rupture and its impact on metal embrittlement
Process engineers strive to recover as much energy as is practically possible from the available process and utility streams within the constraint of the plant. To achieve this goal, traditional—and sometimes non-traditional—methods are utilized. In a steam cracker, light olefins are considered the highest-value products, and utilizing “cold energy,”
Heat Transfer: Designing electric process heater systems for catalytic regeneration
Achieving effective catalyst regeneration requires a process that produces a very high level of heat in a very efficient manner. Over the years, several different approaches have been taken to create this required heat. Traditional steam has been a popular choice, as has heated transfer media. However, these methods have limitations.
Reliability: When slow-rolling machines can cause failures, and how to avoid them
All the book learning in the world will fail if we do not use common sense. We could also say that we need to think things through and should recognize that intuitive logic can lead us astray. If that sounds like semantic banter, let us zero in on three practical field examples that illustrate the issues at hand.
Rethink fired heater design for emissions
As environmental regulations are becoming more stringent on reduced nitrogen oxide and carbon monoxide emissions, burner designs are changing to meet revised regulations. The heater design must complement the chosen burner for optimal performance. Although design duty is considered to be the main focus of the heater design, the range of heater operation and its impact on heater safety and emissions needs are often neglected.
Use submerged combustion systems to efficiently destroy hazardous plant waste
In the production of clean fuels, plastics and other hydrocarbon-based products, refineries and petrochemical facilities generate unwanted (waste) byproducts. Having no market value, the undesired byproducts must be recycled, minimized or eliminated. Depending on the feedstocks, end products and reactant materials, the unwanted materials can be gases, liquids or multiphase materials.
Advantages of using TDL analyzers for safety monitoring in combustion within HPI applications
From refining to chemical production processes, heaters play an essential role in hydrocarbon processing applications.
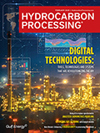
- Ergon to invest $400 MM to expand gasoline production at Vicksburg refinery (U.S.) 4/2
- DB Schenker to use Neste's renewable diesel to decarbonize logistics in Asia 4/2
- U.S. EPA's upcoming proposal on biofuel blending mandates to cover two years 4/2
- ExxonMobil to invest more than $100 MM in Baton Rouge upgrade to produce high-purity isopropyl alcohol 4/2
- Stockholm Exergi to begin building one of the world's largest carbon capture projects using CATACARB Enhanced HPC 4/2
- Quaker Houghton completes its acquisition of Dipsol Chemicals and announces its acquisition of Natech 4/2