Equipment
Preventing wire wooling journal bearing failure
This work details the operation of a 21,000-HP, five-stage barrel pump utilized for seawater injection service.
How the “LLF” condition monitoring technique can improve manufactured product profitability
Technological advances have allowed predictive maintenance (i.e., condition-based maintenance) to overtake preventive maintenance in plant operations. “Look, listen and feel (LLF)” is a condition monitoring technique that improves the reliability of equipment and machinery in manifolds.
Metallurgy solution to prevent polythionic acid stress corrosion cracking in hydroprocessing
Hydrotreating is a staple process found in nearly every refinery. The process removes undesirable feed contaminants, such as sulfur, nitrogen and metals, and saturates olefins and/or aromatics to produce high-quality products.
Editorial Comment: It’s all in the makeup of things
This issue of <i>Hydrocarbon Processing</i> features a topic that has been addressed in sections of the magazine for several decades, but has never been a focal point of the publication. That topic is materials manufacturing.
Use your data to its full potential to prevent outages
In a process plant, the safety system is responsible for the protection of personnel, resources and the environment, by taking the plant to a safe state in the event of a fault. However, is the system capable of contributing more to the plant’s uptime and profitability?
Consider pitot tube pumps for low-flow, high-head applications
Low-flow, high-head pumping requirements in refining and petrochemical plants make up less than 2% of the total pump population. This minor percentage is creating significant reliability concerns, which result in low mean-time between failures (MTBF), as well as high maintenance costs.
Reliability: Dry gas sealing technology replaces segmented carbon rings in small steam turbines
Since the late 1800s, small steam turbines have incorporated bushing-type, single-piece and/or segmented carbon gland components to reduce and prevent steam leakage along the shaft.
Migrating from Fortran to ISA S-88
A major refiner operates two catalytic reforming units for gasoline octane improvement and aromatics production in Texas. In each of these units, five reactors filled with catalyst are operated continuously in series to reform paraffinic hydrocarbons in the presence of hydrogen (H2). During this process, some byproduct coke is unavoidably produced and deposits on the catalyst, which leads to gradual catalyst deactivation.
Advancing export terminal technology: An optimized process for the refrigeration of cryogenic hydrocarbons
Ethane production in North America (NA) has expanded dramatically with the onset of shale production and associated hydraulic fracturing. Ethane concentrations in fractured shale gas are typically 10% or higher vs. a traditional range of 4%–7% in associated gas.
Maximizing energy efficiency in paraxylene production—Part 2
Due to reduced margins, higher energy costs and rising atmospheric carbon dioxide content, energy efficiency has never been more important in refining and petrochemicals. This is particularly true in the modern aromatics complex, which produces paraxylene (pX), benzene and other aromatics from naphtha.
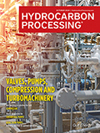
- ExxonMobil plans 1 Blbs/yr of advanced recycling by 2027 11/22
- Gauging the likely Trump effect on U.S. energy and power sectors 11/22
- Russia's Lukoil restoring cracker at NORSI refinery, gasoline output rising 11/22
- Nigeria's local currency crude sales fall short of target, Dangote refinery says 11/22
- U.S. October gasoline imports hit post-pandemic low on slump in European shipments 11/22
- Clean Hydrogen Works awards McDermott FEED contract for Ascension Clean Energy (ACE) project 11/21