Environment
Design considerations when flaring ethylene oxide
The flaring of gases released from normal process vents and safety valve discharges following an overpressure scenario is widely practiced in refineries, petrochemical and chemical plants.
A solution to the IMO 2020 MARPOL Annex VI requirement
On January 1, 2020, a new requirement limiting the sulfur content of marine fuel to a maximum of 0.5 wt% went into effect.
Meeting the Tier 3 challenge with ultra-clean alkylate
The U.S. Environmental Protection Agency (EPA) introduced Tier 3 gasoline sulfur standards in 2017, requiring all U.S. gasoline producers to adhere to an annual 10-ppm average sulfur limit.
Leveraging digital technologies to create the smart renewable diesel facility
Many companies are modifying existing crude refineries or building grassroots renewable diesel facilities to produce drop-in, green renewable diesel from a variety of agriculturally derived triglyceride feedstocks.
Reducing acid consumption: Maximizing sulfuric acid alkylation unit profitability
Alkylation is a process used to produce highly branched isoparaffins from the reaction of lighter olefins and isobutane in the presence of sulfuric acid as a catalyst.
Converting a petroleum diesel refinery for renewable diesel
As refiners consider renewable, low-carbon alternatives, renewable diesel—refined from agricultural products using petroleum refinery processes—is gaining traction.
Down with downtime: Repair complex petrochemical components with selective electroplating
The volatile impact of the coronavirus pandemic hit at the same time the petrochemical industry was entering a downcycle.
A novel polymerization retarder with boosted performance and improved handling characteristics
Styrene monomer production plants continually face a need to slow polymerization rates in the purification section of the production process to increase monomer production rates, reduce polymerization/fouling and tar formation, and protect against equipment plugging, especially in the event of unplanned shutdowns.
Specifying internals in sour water strippers—Part 1
A sour water stripper (SWS) system is a common process in petroleum refineries and other processes where hydrogen sulfide is present.
Successes and challenges installing the first proprietary closed-coke slurry system
The authors’ company<sup>a</sup> licensed a two-drum delayed coking technology process unit to Grupa LOTOS in Gdansk, Poland.
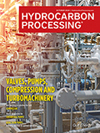
- ExxonMobil plans 1 Blbs/yr of advanced recycling by 2027 11/22
- Gauging the likely Trump effect on U.S. energy and power sectors 11/22
- Russia's Lukoil restoring cracker at NORSI refinery, gasoline output rising 11/22
- Nigeria's local currency crude sales fall short of target, Dangote refinery says 11/22
- U.S. October gasoline imports hit post-pandemic low on slump in European shipments 11/22
- Clean Hydrogen Works awards McDermott FEED contract for Ascension Clean Energy (ACE) project 11/21