Loss Prevention
Case histories of amine plant equipment corrosion problems–Part 1
Lost production from corrosion costs the oil and gas industry more than $1 B/yr.1
Optimizing the dehydration process with advanced process simulation
In the operation of natural gas pipelines, a blockage or leak can cause expensive production losses, damage equipment and pose safety hazards.
Safety in design during mechanical engineering
After a process engineer has completed preliminary documents such as process flow diagrams, material and energy balance, piping and instrumentation diagrams, equipment data sheets, process control philosophies, identifications of the hazardous nature of raw materials, chemicals, byproducts and final products, process equipment layout drawings (plans and elevations), unit plot plans, etc., these documents are issued to other disciplines to carry out further engineering.
Process safety incidents involving simultaneous operations
Some process safety incidents occur as the result of simultaneous or sequential occurrences of operations or activities that interfere or clash with each other.
Demystify hazardous area classification and compliance assessments
As safety becomes increasingly paramount at hydrocarbon processing facilities, so too does the importance of addressing and clarifying the confusion associated with hazardous area classification (HAC) assessments and compliance auditing in Class 1 locations.
Show Preview: ADIPEC
The 20th edition of Abu Dhabi International Petroleum Exhibition & Conference (ADIPEC) will take place 13–16 November at the Abu Dhabi National Exhibition Centre.
Engineering Case Histories: Case 98—Why performing calculations is important to an engineer’s career
Engineering calculations can help an engineer’s career by controlling the risks taken. The author has followed this path.
Automation Strategies: Expanding scope of automation events and alerts
Detecting, reporting and responding to abnormal situations or events are important functional elements of a complete process automation strategy.
Design atmospheric aboveground storage tanks for accident prevention
The design and construction of oil, gas and petrochemical facilities is continuously improving, as increasing compliance with ever-changing codes and standards, such as the American Petroleum Institute (API) and the National Fire Protection Association (NFPA), is resulting in fewer atmospheric above-ground storage tank (AAST) accidents.
Project Management: Bridging the gap in revamp projects—From business need to design basis
Revamp projects are notorious for scope creep, cost and schedule overruns.
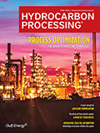
- Essar launches hydrogen power plant at Stanlow refinery (U.K.) 7/16
- Trelleborg partners with Airbus on hydrogen-powered air travel 7/16
- Neste, Mitsubishi Corporation agree on strategic partnership to develop supply chains for renewable chemicals and plastics 7/16
- Vale, Komatsu and Cummins announce collaboration to develop dual-fuel large trucks, powered by ethanol and diesel 7/16
- Mexico–U.S. energy trade value fell in 2023 on lower fuel prices 7/16
- Belarus' Mozyr oil refinery restoring operations after outage due to storm 7/16
- Digital Exclusive: SPECIAL FOCUS: Digital Technologies—Utilize process simulation digital twin to optimize condensate yield
- Digital Exclusive-Flare system design: Liquid pockets in flare headers
- Hydrogen-rich content gasoline: A new concept for paraffinic gasoline reformulation
- Alarm rationalization at Kuwait National Petroleum Company (KNPC) refineries