Environment & Safety
IMO 2020 stability and compatibility headaches
The year 2020 will be a mess from the fuel oil stability and compatibility points of view. The year will be price-driven, so the temptation to “cut corners” is great—meaning that a highly variable number of blend components to manufacture the fuel oil will open a “Pandora’s box” of complex and questionable fuel formulations.
The plight of the modern refinery: Racing to meet IMO 2020 regulations
When Kitack Lim won his second, four-year term as the Secretary General of the International Maritime Organization (IMO) in November 2018, it solidified the organization’s aggressive 2020 deadline for a global < 0.5% sulfur limit on fuel oil used onboard ships. This reduced sulfur requirement, commonly known as IMO 2020, squeezes the oil and gas industry, confounding the medium- and small-size refineries that struggle to produce low-sulfur fuel oil (LSFO), and wracking the nerves of maritime freight shippers facing volatile fuel pricing.
HP Top Project Awards
The editors of <i>Hydrocarbon Processing</i> have identified nine projects that are anticipated to significantly impact the global or regional downstream industries. The winners and nominees of the HP Top Project awards will have a considerable impact on the HPI, whether through CAPEX, satisfying domestic or regional demand, diversifying product offerings, or adding to the resurgence in refining and/or petrochemical processing capacity.
How changes to functional safety standards can optimize fire and gas detection
ANSI/ISA-84 is one of the most influential standards in functional safety and has been a driver for instrumented process safety improvements over the last 20 yr. It is a comprehensive norm covering a wide range of aspects related to functional safety in process industries, including the entire life cycle of designing, implementing and operating safety systems.
Rethink fired heater design for emissions
As environmental regulations are becoming more stringent on reduced nitrogen oxide and carbon monoxide emissions, burner designs are changing to meet revised regulations. The heater design must complement the chosen burner for optimal performance. Although design duty is considered to be the main focus of the heater design, the range of heater operation and its impact on heater safety and emissions needs are often neglected.
Inspection: Best practices for inspecting guyed structures
Guyed structures are common in petrochemicals, oil and gas and chemical industries. Half of the installed flare structures at many facilities are guyed. Various routine inspection programs are in place to examine these structures. This work describes some very basic checks, which should be in place to maintain their mechanical integrity.
Construction
Total plans to take a final investment decision (FID) on the Nigeria LNG expansion project by the end of this year. If greenlighted, the 7-MMtpy LNG train would increase the Bonny Island LNG terminal’s capacity to nearly 30 MMtpy. If built, Train 7 is expected to be operational by 2023.
Editorial Comment: Honoring the industry’s best … take 2!
Due to Tropical Storm Imelda, Hydrocarbon Processing issued its first force majeure in postponing the third annual HP Awards.
Sustainability and the water management company’s role
Water is key to the hydrocarbon processing and chemical processing industries. Yet, it is not an infinite resource, which creates operational, financial and regulatory risks. The true cost of water can include insurance and litigation costs and disposal costs, plus the capital expenditures (CAPEX) and operating expenses (OPEX) of water infrastructure.
Improved cooling system performance begins with data
Refineries consume large amounts of energy and water to refine crude oil into products. Up to 10% of crude oil’s energy content is consumed during processing, and it takes 1.5 bbl of water to process one barrel of crude oil. Refining processes also generate large quantities of excess thermal energy that needs to be expelled into the environment using a once-through or recirculating cooling system.
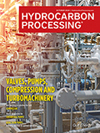
- ExxonMobil plans 1 Blbs/yr of advanced recycling by 2027 11/22
- Gauging the likely Trump effect on U.S. energy and power sectors 11/22
- Russia's Lukoil restoring cracker at NORSI refinery, gasoline output rising 11/22
- Nigeria's local currency crude sales fall short of target, Dangote refinery says 11/22
- U.S. October gasoline imports hit post-pandemic low on slump in European shipments 11/22
- Clean Hydrogen Works awards McDermott FEED contract for Ascension Clean Energy (ACE) project 11/21