Engineering & Design
Maintenance: Zero-based, custom-built, reliability-driven—A new kind of maintenance organization
In the October 2018 issue of <i>Hydrocarbon Processing</i>, the authors published an article—“Improving plant performance by changing a maintenance culture”—describing the first two years of Eastman Chemical Co.’s Longview, Texas site’s journey to maintenance excellence, which began in 2016.
Business Trends: Autonomous operations in process manufacturing—Part 2
The purpose of this article is to demonstrate an autonomous operations (AO) vision, along with its feasibility, by conceptualizing a roadmap where meaningful progress can be achieved in a horizon of 3 yr–20 yr.
Industry Perspective: IRPC Americas ONLINE: A sincere thanks
Each year, <i>Hydrocarbon Processing</i> hosts events to bring together professionals in the oil and gas industry to share ideas and knowledge on the latest advancements in processing technologies and operations.
Mitigate transient/hydraulic surge in liquid pipelines with nozzle check valves
Liquid pipelines often come across hydraulic transients, which can damage pipelines and associated equipment (i.e., pumps, valves, stations, etc.).
Hydrocarbon Processing 2020 Awards WINNERS
<i>Hydrocarbon Processing</i>, the downstream processing sector’s leading technical publication, has announced the winners for its third annual awards.
How valve upgrades can improve tank and terminal facility operations
Tank and terminal facility profitability ultimately rests on a handful of key performance indicators (KPIs). The ability to maximize tank capacity utilization—while minimizing the time it takes to load and unload ships, trucks and rail cars—drives the bottom line. All those transfers must happen quickly and accurately, while avoiding product contamination.
Hydrocarbon Processing Awards 2020—FINALISTS
This special section details all finalists within each category for the fourth annual <ital>HP</ital> Awards. The winners will be announced on Oct. 1.
Driving FCCU value through fresh and flushing catalyst activity modeling
Refiners are continually challenged to maximize economic gain in the face of cost pressures and plant operating constraints. The fluidized catalytic cracking unit (FCCU) plays an integral role in the optimization of the facility. FCC catalyst is often one of the largest budget items in the refinery. Therefore, the balance between FCCU performance and catalyst costs has a significant impact on refinery profitability.
Catalytic processes operation during downturns in aromatics complexes
Paraxylene production is a highly cyclical business that is subject to changes in the global economy and dependent on feedstock costs, alternative dispositions for aromatics, utilities costs and plant locations, among other factors. With the large PX capacity added by recently started crude-to-chemicals complexes and the expected impact of the economic recession on commodities demand, many aromatics complexes face a significant slowdown in the coming months or, possibly, years.
Conventional FCC to maximum propylene production
Fluid catalytic cracking is one of the most important conversion processes used in refineries. This process converts heavy petroleum fractions into lighter, higher-value products, such as gasoline, propylene and others.
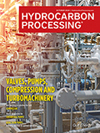
- KBR to provide technology for mega-scale ammonia plant in Angola 11/25
- Indian refiners' October crude processing up over 3% y/y 11/25
- Air Liquide strengthens partnership with TotalEnergies through renewable H2 project in France 11/25
- Hexagon collaborates with Microsoft to enhance industrial operations 11/25
- China issues extra crude oil import quota to teapot refineries 11/25
- McDermott achieves ISO 50001 Certification for energy management at four fabrication yards 11/25