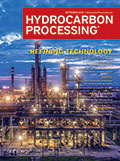
September 2018
Special Focus: Refining Technology
Sulfur oxide additives are typically based on hydrotalcite or magnesium aluminate spinel-type structures. Magnesium alumina is the pickup agent present in the most effective SO<sub>x</sub> additives on the market; therefore, to optimize SO<sub>x</sub> reduction, it is critical to maximize the amount of the critical magnesium component in the fluid catalytic cracking unit (FCCU) in an efficient and cost-effective way.
The following case study describes the early development phases of SOCAR’s ongoing major revamp project at the Heydar Aliyev Refinery (HAR) in Baku, Azerbaijan, and its interface with the associated Azerikimya (AZK) steam cracking complex near Sumgait. References are made to the related SOCAR polymer project in Sumgayit, as well.
To meet increasingly stringent specifications for cleaner gasoline and to produce more clean fluid catalytic cracking (FCC) naphtha with lower olefins, a novel FCC technologya for maximizing isoparaffins was developed in the late 1990s. The technology’s principal is based on the formation and conversion of olefins in two different reaction zones.
This work is a follow-up article to “Automate furnace controls to improve safety and energy efficiency,” which was published in the June 2014 edition of <i>Hydrocarbon Processing.</i>
Change involves risk. Many fluidized catalytic cracking units (FCCUs) can be operated more profitably, but changes to achieve more efficient operations can be risky.
Maintenance and Reliability
While electrical equipment typically has a lengthy lifespan, it is not meant to last, or be relevant, forever.
The role of octane boosters on the corrosivity of petroleum products for gasoline/diesel engines has attracted more attention in the auto fuel market due to the depletion of fossil fuels in the world’s feedstock.
Unplanned outages due to mechanical failures can cost millions of dollars of lost production time for oil and gas companies.
Process Optimization
Aromatics are fundamental petrochemical compounds used as raw materials to manufacture hundreds of polymers, solvents and additives; these, in turn, are used to make consumable products that people use every day.
Hydrocarbon Processing Awards
<i>Hydrocarbon Processing,</i> the downstream processing sector’s leading technical publication, has announced the winners for its second annual awards.
Heat Transfer
One of the most misunderstood and misused components of conductive steam tracing systems is heat transfer compound (HTC).
Environment and Safety
In today’s economic environment, new capital spending is harder to find than loose change buried under the couch cushions.
Recent storage tank and industrial plant explosions around the world bring into focus the importance of engineering and building standards.
By January 30, 2019, the 40 CFR Part 63 Subpart CC rule by the US Environmental Protection Agency (EPA) requires petroleum refinery owners or operators of flares used as control devices for emissions points to meet the requirements of §63.670, regardless of the construction date of the flare.
Water Management
Refiners are becoming increasingly dependent on opportunity crudes to stay competitive and support margins in the industry’s present uncertain state.
Columns
Readers have witnessed that throughout the life of the publication, <i>Hydrocarbon Processing</i> has always published information on new technologies to increase efficiency, safety and profitability in downstream processing operations, while introducing techniques to decrease environmental footprint and emissions and produce high-quality, clean fuels and petroleum products for consumers around the world.
Making the vendor-manufacturer your technology provider has been our consistent advice to the user industries; we have recommended this highly effective approach for many decades.
The Chinese refining industry is on the verge of massive production cuts and consolidation. A new tax rule aimed at curbing alleged tax evasion by independents and the end of an era of liberalization in the industry are driving the downsizing.
The American Institute of Chemical Engineers (AIChE) is made up of more than 60,000 members from more than 110 countries.
For refiners, the future is full of uncertainty. Due to market forces—e.g., the macroeconomics of oil and gas supply and demand, the increasing demand for petrochemicals and new marine low-sulfur fuel requirements—organizations are faced with many business challenges that require increasingly flexible operations.
The tiny company town of Sinclair sits in south-central Wyoming.
The combination of US tax reforms and changes to global bunker fuel specifications in 2020 as part of the International Maritime Organization’s (IMO’s) new regulations are set to turn the US oil and gas downstream into a cash cow.
Trends & Resources
According to multiple industry reports, the global refining sector will add between 7 MMbpd and 8 MMbpd of new crude distillation unit (CDU) capacity by the early 2020s.
In April, ExxonMobil launched its <i>2018 Basestocks Industry Pulse Report.</i>
US margins recorded losses as crack spreads declined for all products except fuel oil, despite lower refinery crude intakes.
According to <i>Hydrocarbon Processing</i>’s Construction Boxscore Database, there are nearly 470 active refining projects around the globe.
BCCK Holding Co. (BCCK) has appointed Bob Swann as Director of project management and controls.
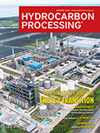
- BPCL and National Sugar Institute collaborate to advance sweet sorghum as a sustainable biofuel source 2/21
- Resynergi secures $18 MM to accelerate plastic recycling innovation 2/21
- LiqTech receives supplier approval for water treatment system for WinGD dual-fuel engine 2/21
- Japan's Eneos shuts 141,000-bpd Sakai CDU after a fire 2/21
- Russia's idle oil refining capacity estimated 82% up in February 2/21
- U.S. refiners mull switch to alternative lighter crudes amid Trump tariff fears 2/21