Corrosion
Pace CCS, Foxconn, TEWE to solve critical CCS challenge
Pace CCS, a global leader in CCS design, has announced a landmark collaboration with Foxconn, the world-renowned technology manufacturer, and TEWE [Taiwan East West Enterprises (CHEMA) Ltd.], a nearly century-old sales and service provider to Taiwan’s industrial sector. Together, the three industry leaders are developing a first-of-its-kind chemical injection unit designed to address the most pressing challenge in CCS: the removal of key impurities from carbon dioxide (CO2) streams that can cause corrosion in CCS networks.
Sherwin-Williams expands global core product offering for customers worldwide
Sherwin-Williams Protective & Marine has unveiled new Global Core coatings that include an inorganic zinc primer, epoxy primer, epoxy intermediate coat and urethane topcoat. These versatile coatings can be used to create multi-layer coating systems for corrosion protection and aesthetics for a wide range of applications
New Sherwin-Williams Advanced Energy Barrier eliminates threat of corrosion under insulation
Sherwin-Williams’ Heat-Flex® Advanced Energy Barrier (AEB) tackles corrosion under insulation (CUI), effectively eliminating the costly and dangerous phenomenon of steel assets corroding underneath insulation systems. The coating replaces the bulky mineral-based insulation that is traditionally used on storage tanks, process vessels and piping to retain process heat.
Hydrogen cyanide in amine systems
Mass transfer rate-based simulation has been used to study hydrogen cyanide ingress and accumulation in amine systems in unprecedented detail. In this article, the chemistry, prevention and possible mitigation using water washing arrangements and reflux purging are discussed quantitatively.
Reduce costs by following grab sampling best practices
Accurate grab sampling practices are necessary to validate the quality of chemical products with precise compositions. Operators must follow proper procedures to avoid compromising the sample. Otherwise, the result may be an inaccurate analysis of their product, leading to quality lapses and potentially costing a facility thousands of dollars in revenue.
Improving ammonia production sustainability
While approximately 70% of ammonia production is used to make fertilizers, it is also identified as the largest carbon dioxide (CO2)-emitting chemical industry process. This article examines several novel technologies to improve the sustainability of the ammonia production process.
Use advanced thermal insulative coatings to improve safety, maintain access and protect against corrosion
Throughout refineries, petrochemical plants and offshore oil and gas platforms, personnel are often required to work near equipment that operates at high temperatures. Protecting those workers from skin-contact burns has typically involved two approaches: implementing physical barriers and covering the hot assets with insulation and cladding. This article details how thermal insulative coatings can be used to improve safety and guard against corrosion.
Refinery/petrochemical makeup water treatment: A general guide for technical personnel—Part 3
A very important—and sometimes overlooked—unit operation within hydrocarbon processing facilities is makeup water treatment for steam generators and other processes. Many cases have been documented in which makeup system upsets have led to boiler tube failures that partially or completely shut down unit processes. The three parts of this article (August, September and October 2024) serve as a guide for those employees who may be on a steep learning curve when it comes to makeup system understanding.
Validate skin temperature in refractory-lined pipes using manual calculation vs. FEA analysis
Accurately estimating skin temperature and understanding the impact of refractory lining on thermal performance are crucial aspects of piping system design, operation and maintenance. By recognizing the multifaceted role of refractory lining in enhancing operational efficiency, mitigating risks and extending the lifespan of industrial piping systems, industries can optimize their processes and ensure the reliability and safety of their infrastructure.
Meet gasoline quality and process safety requirements through new alkylation technologies
The catalytic alkylation process is very attractive to countries with high gasoline consumption and a sizable availability of LPG. This process can produce high-octane gasoline with low levels of contaminants, although there are high capital investment and operational costs associated with this technology.
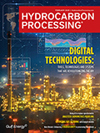
- Phillips 66 Independent Board Director pens letter to shareholders regarding dispute with Elliott Investment Management 3/28
- Russia increases fuel, diesel supply to Bolivia amid rising energy crisis 3/28
- Cenovus refinery in Ohio (U.S.) plans to shut multiple units for six weeks of work 3/28
- Motiva Texas refinery (U.S.) preparing second attempt to restart FCCU 3/27
- bp plans to sell its mobility and convenience business in Austria 3/27
- BASF starts up its first plant for recycled polyamide 6 3/27