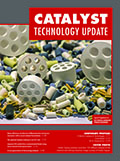
Catalyst Technology Update
Raise efficiency of ultra-low SHR production of styrene monomer with a novel catalyst formulation
The production of styrene monomer from ethylbenzene requires superheated steam as an energy source, as well as dehydrogenation catalysts to facilitate the reaction. As steam generation poses the highest influence on production costs, significant effort has been devoted to optimizing process design.
The optimal catalyst makeup in an FCC unit
Fluid catalytic cracking (FCC) is one of the key process technologies in the refining industry. The FCC unit increases refining margins by upgrading low-value streams, such as vacuum gasoils or atmospheric and vacuum residues, to more valuable products, such as propylene, butylenes and high-octane naphtha.
Improve FCC yields from contaminated feeds using boron-based nickel passivation
The drive to improve refinery margins leads to the processing of heavier, more contaminated crude and, consequently, an increasing amount of contaminants in fluid catalytic cracking (FCC) feedstock. Of these, nickel (Ni) deposits on the FCC catalyst and catalyzes dehydrogenation reactions, producing unwanted hydrogen (H2) and contaminant coke. These effects diminish the profitability and operability of the FCCU, creating strong demand for Ni passivation technology. Ni passivation is especially beneficial when the FCCU operates at the wet gas compressor (WGC), regenerator temperature limit, or air limit.
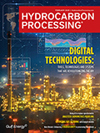
- Dow Chemical, X-energy to advance nuclear project at Dow's Seadrift chemicals facility (U.S.) 3/31
- Varo buys Swedish refiner Preem in bet on biofuels 3/31
- Cenovus refinery in Ohio (U.S.), plans to shut multiple units for 6 weeks for maintenance 3/31
- INEOS Enterprises completes the sale of INEOS Composites to KPS Capital Partners for €1.7 B 3/31
- Willis Sustainable Fuels selects FT CANS to boost sustainable aviation fuel production in the UK 3/31
- Uganda signs deal with UAE investment firm over 60,000-bpd oil refinery 3/31