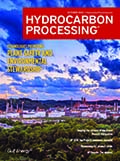
October 2020
Special Focus: Plant Safety and Environment
For the petrochemical industry, the U.S. Gulf Coast (USGC) has the locational advantage of proximity to cheap feedstock, and to an abundance of pipeline infrastructure and terminals for export markets.
Process cooling usually comprises the largest part of the water footprint of a refinery or petrochemical plant.
Emissions from flares worsen air quality and produce waste gas. A flare gas recovery system is designed to facilitate CO<sub>2</sub> reduction.
Abnormal situations in refining and petrochemical plant operations can interfere with plant reliability and efficient operations, especially for highly complex processes.
A process plant’s pressure relief and flare systems are critical safety elements.
Toxic risk preferably should be controlled according to Kletz’s inherent safety principle, which consists of some preventive golden rules, notably <ital>minimize, substitute, moderate</ital> and <ital>simplify</ital>.
Hydrocarbon Processing Awards WINNERS 2020
<i>Hydrocarbon Processing</i>, the downstream processing sector’s leading technical publication, has announced the winners for its third annual awards.
Refining Technologies
Part 1 of this article, which appeared in the September issue, discussed various aspects of evaluating options that enable an existing refiner to make investment decisions to optimally diversify into petrochemicals through integration. Part 2 will detail a case study that illustrates the synergies of refinery-petrochemical integration through a propylene recovery unit from an FCC-based refinery, as well as financial, configuration and sensitivity analyses.
Catalysts
Fluid catalytic cracking (FCC) is one of the most important conversion processes used in petroleum refineries and has been in use for more than 75 yr.
Process Control, Instrumentation and Automation
With best available technology, how much practical reduction in giveaway can be achieved, with the caveat that there is no such thing as “zero error” in value measurements? Also, can those numbers change if inline blending is used? This article seeks to answer both questions.
Valves, Pumps and Turbomachinery
Liquid pipelines often come across hydraulic transients, which can damage pipelines and associated equipment (i.e., pumps, valves, stations, etc.).
Columns
<i>Hydrocarbon Processing</i> has announced the nominees for its annual Top Projects awards.
Technical writers and other communicators occasionally have cause to think about matters having to do with publication practices and why some publications have higher quality or more reader-relevant illustrations than others.
In the October 2018 issue of <i>Hydrocarbon Processing</i>, the authors published an article—“Improving plant performance by changing a maintenance culture”—describing the first two years of Eastman Chemical Co.’s Longview, Texas site’s journey to maintenance excellence, which began in 2016.
During this unprecedented industry crisis spurred by the COVID-19 pandemic, the process industry’s response has been multi-faceted, showing its generosity and humanitarian side, as well as its collective resilience to an environment filled with formidable challenges.
Maintaining the structural integrity of a pipeline is a significant investment of time and resources for organizations in the oil and gas industry.
Brazil’s refining industry is on the verge of large-scale change. Its recent steps toward de-monopolization and liberalization, as well as the divestment of refining assets by state-owned oil major Petrobras, are propelling Brazilian refining in a more attractive direction for investment.
The main objective of any industry is to operate as close as possible to the point where profits are maximized.
Hydrocarbon processing businesses increase profitability and survivability by optimizing production and/or reducing expenses to maximize profitability—or in the extreme, cash flow.
Trends and Resources
Each year, <i>Hydrocarbon Processing</i> hosts events to bring together professionals in the oil and gas industry to share ideas and knowledge on the latest advancements in processing technologies and operations.
The purpose of this article is to demonstrate an autonomous operations (AO) vision, along with its feasibility, by conceptualizing a roadmap where meaningful progress can be achieved in a horizon of 3 yr–20 yr.
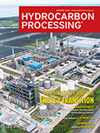
- BPCL and National Sugar Institute collaborate to advance sweet sorghum as a sustainable biofuel source 2/21
- Resynergi secures $18 MM to accelerate plastic recycling innovation 2/21
- LiqTech receives supplier approval for water treatment system for WinGD dual-fuel engine 2/21
- Japan's Eneos shuts 141,000-bpd Sakai CDU after a fire 2/21
- Russia's idle oil refining capacity estimated 82% up in February 2/21
- U.S. refiners mull switch to alternative lighter crudes amid Trump tariff fears 2/21