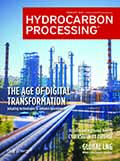
February 2020
Special Focus: Digital Transformation
Gas processing, liquefaction, oil refining, bulk petrochemicals and chemicals plants represent a large population of frontline engineers and technical managers. Their professional lives will become increasingly impacted by the growing adoption of disruptive digital technologies and digital platforms.
Today’s tools are often specialized for a certain type of task; however, they often lack the connectivity that would enable the easy comparison and cross-reference of asset information. Engineering tools are well suited for design and build phases, but may be less suited for use in operations and maintenance.
The term Industry 4.0 refers to the fourth industrial revolution. Widely hailed as a new level of organization and control over the entire value chain of the lifecycle of products, Industry 4.0 is geared toward progressively personalized customer requirements.
The refining industry is facing increased pressures, such as crude oil supply changes, changing product distributions and increasing regulations. These pressure points create a highly competitive market where refiners are looking for options that include digitally transforming operations and adapting new technologies to enhance safety and improve uptime, flexibility and efficiency, while securing their competitive position in a dynamic market. Improving personnel and process safety remains a top focus area for refiners.
Maintenance and Reliability
In many refineries and petrochemical plants, air fan coolers (AFCs) become a major bottleneck to increasing plant capacity. Many plants suffer from lower heat duty than designed, especially during the summer months, which can lead to lower plant capacity.
Process tubes in refining applications are typically steel alloy (ASTM A335 P22, P5 or P9), which contain 2.25%, 5% and 9% Cr, respectively. These grades oxidize at operating temperatures, and scale will grow continuously on the surface, often reaching 2 mm in thickness in higher-temperature/high-heat-flux units. The layers of scale are very insulating and represent a significant barrier to conductive heat transfer to the process.
Process Controls, Instrumentation and Automation
Advanced process control (APC) projects are supervisory programs that are often thought of as a layer of control above the base regulatory control for a process. The benefits of APC include increased throughput, reduced variation, constraint avoidance, etc., and can be combined to represent a daily economic-equivalent benefit for the application—the same anticipated benefit that led to the justification of the APC installation. Several articles report that after 18 mos–24 mos, more than half of APC installations are performing at either pre-installation levels or have been removed.1,2,3 Although diverse reasons exist for the performance shortfall, a primary reason is that the process characteristics drift from those that generated the controller model.
Cybersecurity
As digitalization accelerates in today’s downstream refining and petrochemical facilities, operators need to stay ahead of ever-growing cyber vulnerabilities in the operational technology (OT) layer—prime targets for threat actors—that may not be covered by traditional IT safeguards. Unfortunately, too often, that is not the case for a variety of reasons.
Valves, Pumps and Turbomachinery
In recent case studies, unexpected and unmonitored torsional vibration resulted in sudden failures, costly downtime and potential safety hazards. Part 1 of this article, which appeared in the January issue of <i>Hydrocarbon Processing,</i> examined the origins of torsional vibration and case histories to drive an understanding of the unmonitored risk existing at many industrial sites.
Environment and Safety
Many industrial facilities, especially those in the chemical, oil and gas and petroleum industries, involve inherent risks in operations due to the processing of material that is hazardous in nature. It is necessary to precisely identify and analyze hazards, operability issues, associated risks and consequences.
Columns
What is the future of refining and petrochemical operations? One trend that has been the focus of many articles, whitepapers and conference presentations is the digital transformation of the hydrocarbon processing industry (HPI).
You may recognize the “pre-owned” pump in FIG. 1 as an axially split, between-bearing, multistage model. Chances are that half of its impellers face right-to-left and half of them face left-to-right. In that case, there must be an internal seal or bushing that limits leakage flow from the pump’s higher- to lower-pressure sections. There must also be porting or piping that takes flow from the discharge of the lower-pressure section to the suction of the higher section.
The science of project planning has something of a tenuous reputation. How often do large oil and gas capital expenditure (CAPEX) projects really come in according to plan? Almost never. Indeed, 30% of respondents to a 2018 PWC survey said they had experienced cost overruns of 10%–50% on their Middle East capital projects.
2019 was a year of successes within the recycled polyester (RPET) industry.
Internal inspections of pressure equipment involve a full inspection of the equipment. Inspection engineers and inspectors depend heavily on internal inspections to retrieve useful data, which includes information on active degradation mechanisms, corrosion rates, remaining equipment life, failure occurrences and failure expectations, among other critical details.
A 15-yr rise in U.S. exports of refined products continued in 2019 with the nation exporting more than ever, underscoring the importance of these products to fueling a growing world. In the latter half of the last decade, U.S. petrochemical production capacity increased—with more than $20 B invested in domestic petrochemical projects in the last 2 yr alone—and exports of petrochemicals and petrochemical feedstocks rose, as well.
With the ever-increasing speed of technology innovation around the Industrial Internet of Things (IIoT) and cloud offerings, industrial manufacturers are evaluating how these new solutions can impact their daily operations. Specifically, they are looking at how these innovations enable real-time, actionable insights across processes, assets and the workforce. These insights allow for quicker and more informed decisions, thereby driving efficiency and profitability.
Welcome to the future! The plant runs fully automated; robots glide silently back and forth, ensuring an optimized process; and your maintenance technician—with a few keystrokes—can tell you exactly how each piece of equipment is running. The promise of the Industrial Internet of Things (IIoT) has been delivered.
Goldman Sachs predicts that the augmented reality (AR) industry will become an $80-B market by 2025. At first glance, this is probably not a startling number—not when you consider the size of the entertainment industry and how immersed AR has become in video games, movies and the various ways it is being used by smartphone apps.
Trends and Resources
In December 2019, <i>Hydrocarbon Processing's</i> launched its new podcast series: The Main Column. The podcast series will feature the latest in hydrocarbon processing industry (HPI) trends, technology developments, engineering and operations.
Expanding LNG supply worldwide will continue to dominate the changing landscape of the natural gas industry and gas trade. By 2040, LNG is expected to account for more than 15% of global gas consumption, after overtaking interregional pipeline deliveries in the late 2020s.
US refinery margins continued the downward trend, but the negative impact of the weaker domestic fuel market was partly offset by a rise in total product exports.
<i>Hydrocarbon Processing's</i> Construction Boxscore Database is tracking more than 1,430 projects around the world.
Nigeria LNG (NLNG), a consortium comprised of Nigerian National Petroleum Corp. (NNPC), Shell, Total and Eni, has greenlighted the expansion of the Bonny Island LNG terminal.
Analytical Systems Keco introduces the 205L Laboratory H2S in Liquids Analyzer that quantifies hydrogen sulfide (H2S) in crude oil, fuel oil, naphtha, water, diesel and gasoline. The removal of H2S in crude oil, condensate and other liquid products before transport or storage is imperative to reduce the risk of health and safety issues, as well as product quality control. In addition to providing high precision in testing for H2S in crude oil, the analyzer is fast, offering results within 10 min.–15 min.
Motion Industries Inc. has named Chris Pacer as VP of the company’s Central Group. Mr. Pacer has spent the last 22 yr with Motion Industries in various key roles after joining the company as a certified fluid power specialist. He was promoted to Branch Manager of the various markets within Northern Ohio and then joined the company’s corporate accounts team before being promoted to his latest position of Detroit Division VP and General Manager. In that role, Mr. Pacer was responsible for the further development and overall growth of 22 branch operations and one service center.
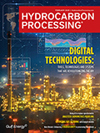
- KazMunayGas starts building polyethylene plant with Sinopec, SIBUR 4/1
- Blue Tide, Shell Lubricants complete re-refining facility to develop high-performance lubricants 4/1
- Lummus successfully starts up PFAS demo unit to destroy "forever chemicals" 4/1
- Solvay partners with Cavalinho to reduce emissions at Brazilian chemical plant 4/1
- Dow Chemical, X-energy to advance nuclear project at Dow's Seadrift chemicals facility (U.S.) 3/31
- Varo buys Swedish refiner Preem in bet on biofuels 3/31