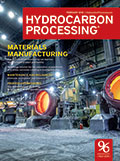
February 2018
Special Focus: Materials Manufacturing
Hydrotreating is a staple process found in nearly every refinery. The process removes undesirable feed contaminants, such as sulfur, nitrogen and metals, and saturates olefins and/or aromatics to produce high-quality products.
The standard practice recommended for high-pressure vessels with heavy wall thickness requires the implementation of weld joint preparation with a narrow gap technique. This generally calls for a two-beads-per-layer sequence, along with the use of the submerged arc welding (SAW) process.
Technological advances have allowed predictive maintenance (i.e., condition-based maintenance) to overtake preventive maintenance in plant operations. “Look, listen and feel (LLF)” is a condition monitoring technique that improves the reliability of equipment and machinery in manifolds.
Maintenance and Reliability
Multiple mechanical seal failures in a crude distillation unit (CDU) resulted in total losses of $3 MM in a refinery since its startup in January 2015. The maximum seal life achieved did not exceed 6 mos, which was much shorter than the American Petroleum Institute (API) 682 “Advancements in Mechanical Sealing” goal of 3 yr of seal life.
Low-flow, high-head pumping requirements in refining and petrochemical plants make up less than 2% of the total pump population. This minor percentage is creating significant reliability concerns, which result in low mean-time between failures (MTBF), as well as high maintenance costs.
Hydrocarbon plants use a system of pipes of various sizes, pressures and temperatures. Sometimes these pipes have pulsating flows that result in piping system vibration. These piping systems must be designed for a high degree of reliability, which requires a comprehensive piping stress analysis for thermal, sustained, occasional and dynamic loading conditions.
Environment and Safety
In a process plant, the safety system is responsible for the protection of personnel, resources and the environment, by taking the plant to a safe state in the event of a fault. However, is the system capable of contributing more to the plant’s uptime and profitability?
A process engineer must complete the preliminary preparations of process flow diagrams, material and energy balances, piping and instrumentation diagrams (P&IDs), process control philosophy, and identification of the hazardous nature of raw materials, chemicals, byproducts and final products.
Bonus Report: LNG Developments
Over the past several years, new gas processing/LNG capacity has surged in nearly every region. Growth on both the supply and demand sides has resulted in the announcement of billions of dollars of capital investment around the world. Millions of tons of new LNG import and export capacity have begun operations, with hundreds of millions of tons still under development.
The production of liquefied natural gas (LNG) requires a number of stages to effectively purify the feed gas. These stages are essential to maintain continuous operation and to meet product specifications. Liquid and solid contamination issues are common in many feed gas purification operations and can cause severe problems with equipment fouling, leading to additional expenses in maintenance and equipment repair, reduced production capacity and even unscheduled shutdowns.
Process Optimization
Reliance Industries Ltd. (RIL) operates the world’s largest refinery complex, with a combined crude processing capacity of 1.24 MMbpd that is split between two refineries: a Domestic Tariff Area (DTA) refinery and a Special Economic Zone (SEZ) refinery in Jamnagar, India.
First, we must consider the background: Why is optimization of refinery process units so common and so necessary, and what analytical tools exist to help?
The global refining industry is constantly evolving and responding to new crude supplies and sources, more stringent fuel/product specifications, perpetually changing demand patterns and other global and regional trends. Increased competition from large, efficient refineries is forcing small- to mid-sized refiners to rethink their strategies to remain competitive.
Columns
This issue of <i>Hydrocarbon Processing</i> features a topic that has been addressed in sections of the magazine for several decades, but has never been a focal point of the publication. That topic is materials manufacturing.
Most centrifugal pump designs include replaceable rotating wear rings on the impeller (impeller wear rings) and stationary wear rings inside the casing (case wear rings). Although pump wear rings are simple components, they can have profound impacts on pump reliability, efficiency and safety. These wear rings serve three purposes:
A questioning attitude is a trait that all engineers should cultivate. Most scientific inventions have resulted from such an attitude, and the classic example is Sir Isaac Newton’s story of developing the law of gravity while seeking the answer to the simple question of why an apple had fallen from a tree.
Machinery professionals are constantly searching for ways to improve the reliability or capabilities of process machines. However, the level to which improvements can be economically justified is limited.
A variety of aliphatic hydrocarbon solvents and thinners are being consumed globally. Preferences for one solvent over another depend on various factors, such as solvency, evaporation rate, boiling point, viscosity and surface tension.
Businesses throughout the oil and gas industry use technical standards—specifications, test methods and guides, among others—as part of the foundation for developing the best processes and products. For example, standards are deeply integrated into how petroleum is refined, tested, stored and transported.
As asset performance management (APM) continues to evolve, the introduction of new methods and cutting-edge technologies are rapidly increasing its bottom-line value. Cloud computing, data science and machine learning are among the technologies that are now being integrated with automated methodologies directly into APM solutions. As a result, operators and engineers now have advanced analytical capabilities at their fingertips.
Trends and Resources
According to <i>Hydrocarbon Processing’s</i> Construction Boxscore Database, more than 870 new projects have been announced since 2015.
The opportunities for industrial analytics within the chemical industry, and how advances in machine learning can impact revenue, operations, employee safety and capital investments, are analyzed here.
Record low temperatures in the eastern US strengthened the diesel market but extended the downward trend in refining margins.
<i>Hydrocarbon Processing’s</i> Construction Boxscore Database is tracking more than 1,700 projects around the world.
Amy Hebert has joined Haldor Topsoe A/S as Deputy CEO and Executive VP (EVP), Chemicals.

- Colombia's Ecopetrol to invest up to $700 MM in SAF production plant 4/2
- Ergon to invest $400 MM to expand gasoline production at Vicksburg refinery (U.S.) 4/2
- DB Schenker to use Neste's renewable diesel to decarbonize logistics in Asia 4/2
- U.S. EPA's upcoming proposal on biofuel blending mandates to cover two years 4/2
- ExxonMobil to invest more than $100 MM in Baton Rouge upgrade to produce high-purity isopropyl alcohol 4/2
- Stockholm Exergi to begin building one of the world's largest carbon capture projects using CATACARB Enhanced HPC 4/2